コードレススティック掃除機の新モデルが登場
パナソニックの掃除機製造拠点「八日市工場」でみた“品質”と“信頼性”の追求
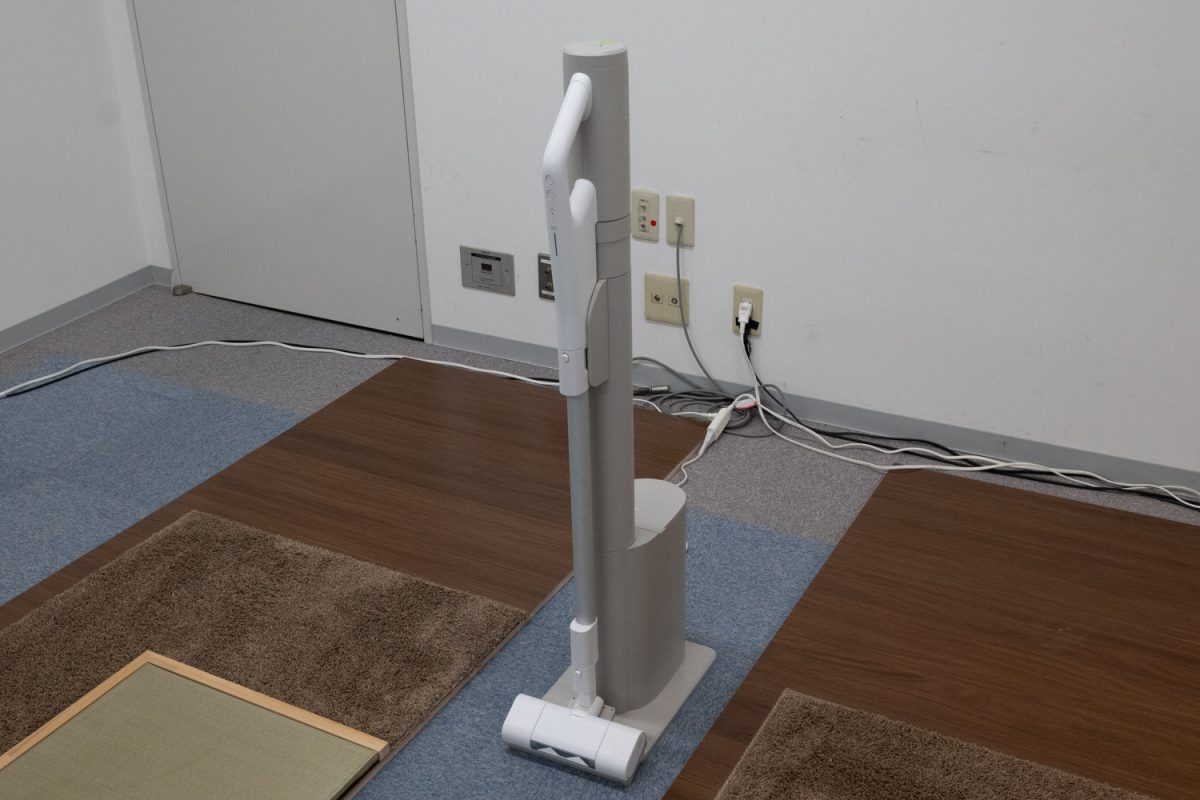
パナソニックは、マイクロミスト機能を新搭載するコードレススティック掃除機「MC-NX810KM」を10月下旬に発売した。このタイミングに合わせて同社では、掃除機を製造する一大拠点、八日市工場(滋賀県)への合同取材会を実施。同製品の製造現場が一部公開された。
MC-NX810KMでは、クリーナーのヘッド部分からマイクロミストを噴霧することで、フローリングなどにある “見えないほど小さいくぼみ” のゴミも除去できるという新機能を搭載。フローリングワイパーのように僅かな水分で水拭きするような効果が得られ、素足でも床のざらつきを感じにくい掃除が行えることがアピールされている。
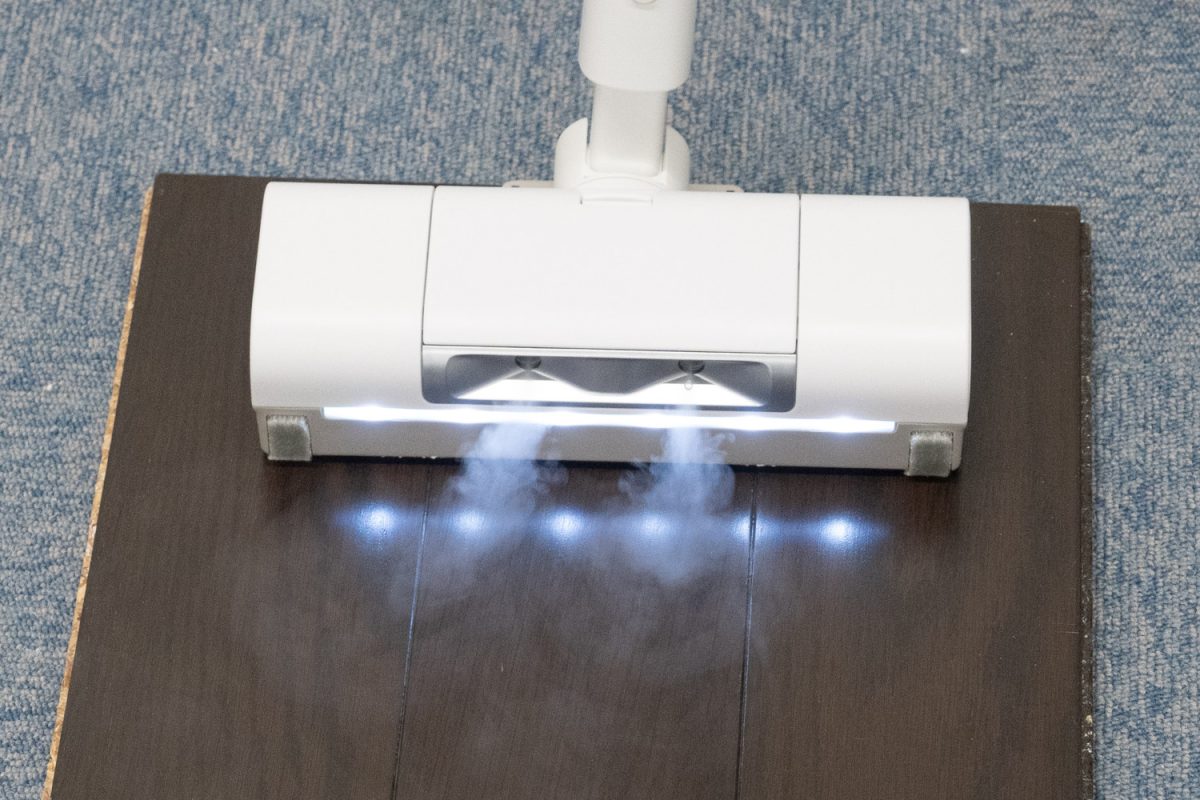
またセパレート型を採用するため、クリーンドックに約3.5か月分のごみを自動収集でき、吸い取ったゴミを毎回捨てる手間が不要。加えて、ヘッド部にはより絡みづらく改良した「からまないブラシPlus」を採用するなど、基本的な清掃性能も進化させている。なお、マイクロミスト機能をより安価に選べる選択肢として、クリーンドックのない「MC-SB70KM」(想定税込6万円前後 ※NX810KMは想定税込9万円前後)もラインナップされている。
1971年から八日市工場で掃除機を製造
本製品は、滋賀県にある八日市工場にて製造されている。この工場はパナソニックのクリーナー製品の専用工場として、1971年から稼働。スティック掃除機だけでなく、キャニスター掃除機、ロボット掃除機も製造している。また、黒板拭きクリーナーや家庭用生ごみ処理機の製造も担っているという。従業員は約460人、敷地面積は約86万平方メートル。
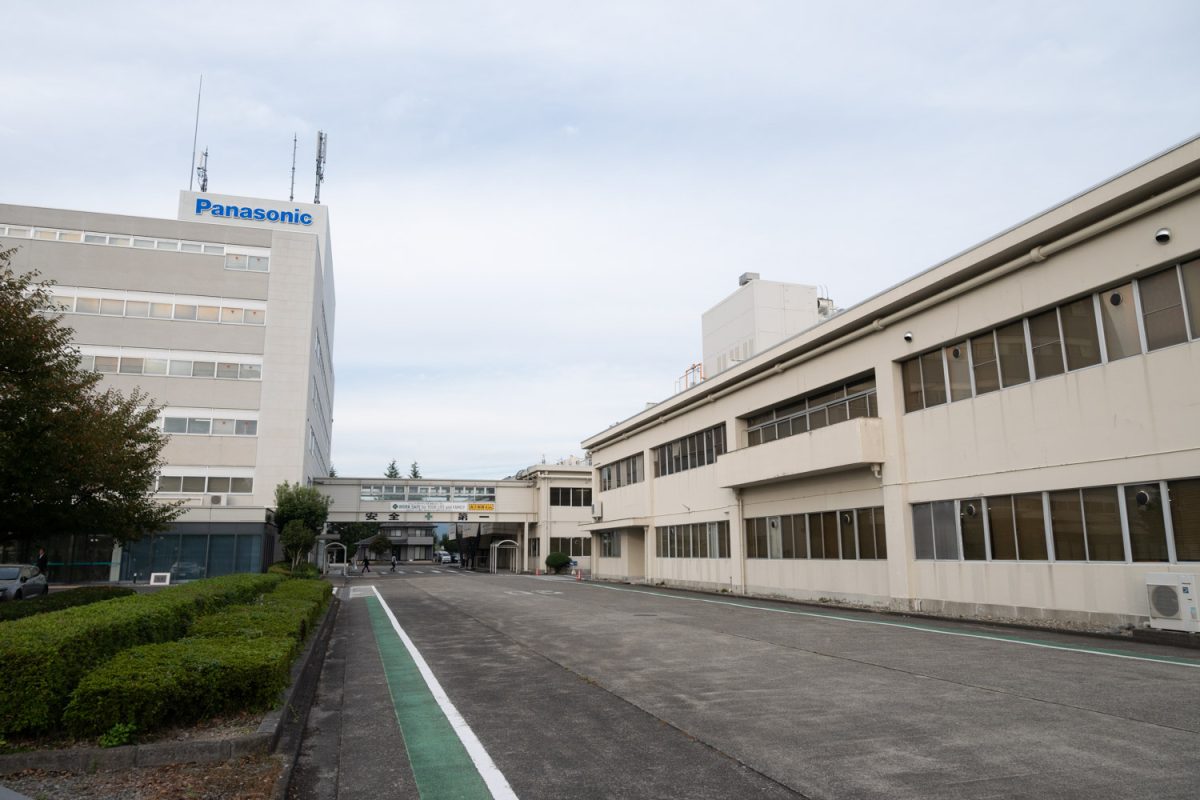
同社が掃除機を始めて市場に投入したのは1954年。当初は金属製の筐体が用いられていたが、1971年に登場した「隼」から樹脂を採用。以来、樹脂成形技術や樹脂素材を活用した軽量化技術を進化させてきたという。なお、八日市工場はクリーナー事業におけるグローバルのマザー工場という位置づけ。ほかには中国とマレーシアにも工場があり、そちらでは主に海外向けのクリーナー製品が作られている。
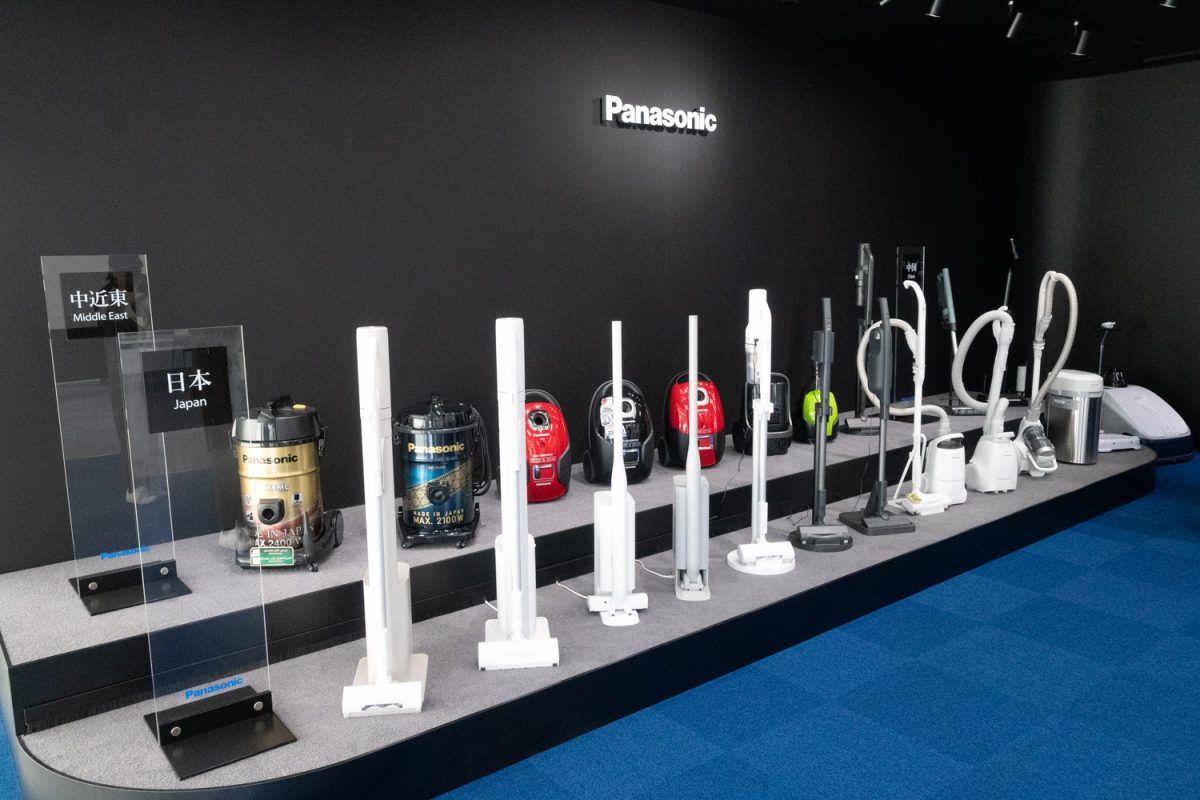
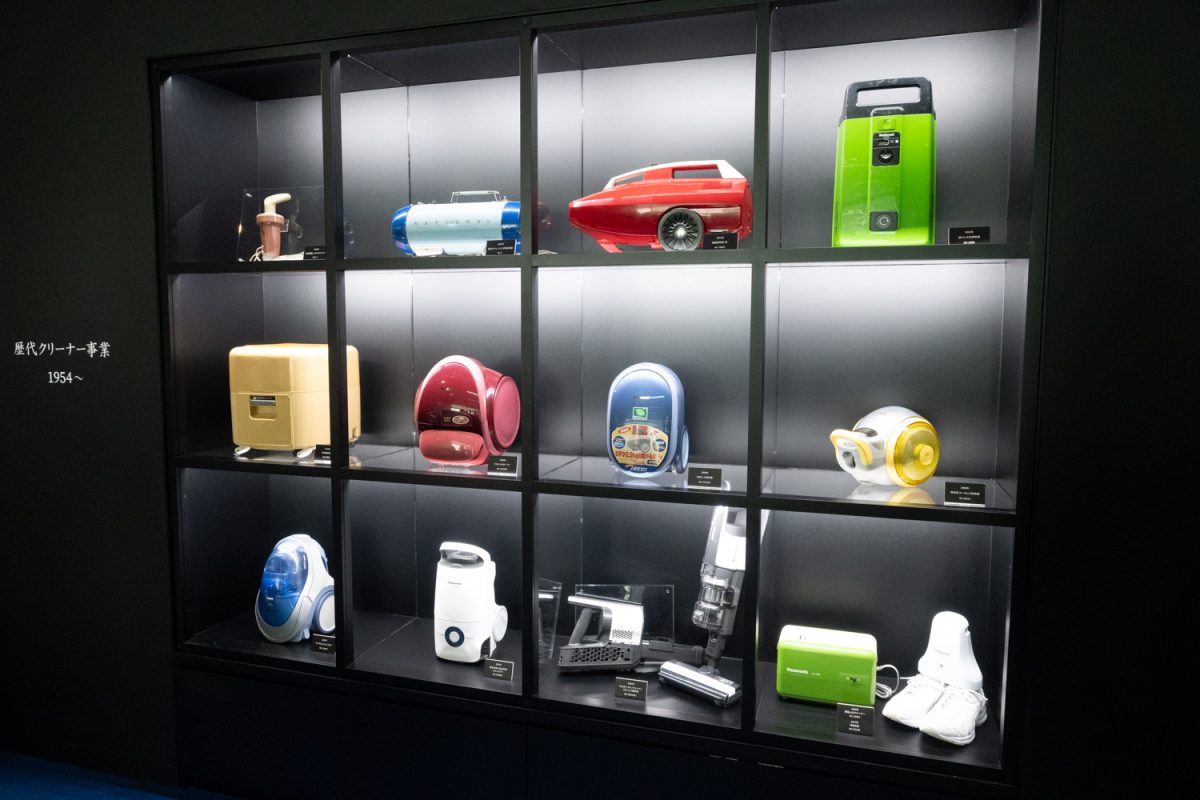
八日市工場の強みとしているのが、商品企画から設計、樹脂成形、製造までを一気通貫で行えるという体制。これにより、生活スタイルや市場の変化にもスピーディに対応できるという。また、長い経験で培った樹脂の成形技術も大きな強みであり、樹脂の塊である掃除機において、安定した品質を保つことに繋がっているそうだ。
工場の敷地内には大きくわけて3つの建物、6階建ての管理棟と組み立て棟、製造棟が設けられている。加えて敷地内には、一軒家を模した「生活研究ハウス」も建てられ、実家庭に近い状態での使用性評価も実施。「日本のお掃除を一番知っているブランド」を目指し、種類の違う畳(い草/和紙/樹脂/琉球間など)やフローリングを、日本各地で収集した土埃のサンプルで継続的に検証を行っているという。
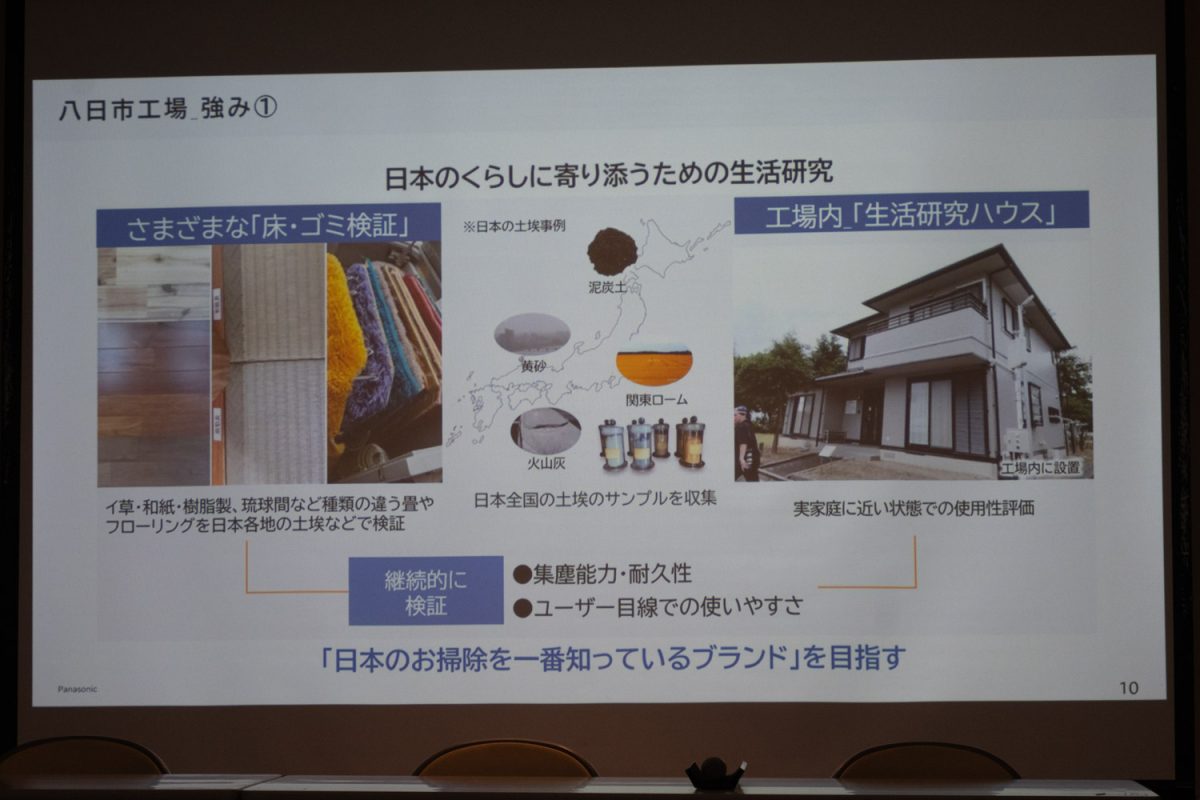
樹脂成形から組み立てまでワンストップ
では、MC-NX810KMの製造工程に話を移そう。まず同工場の成形製造課では、素材である樹脂の着色方法に「ドライカラー方式」を採用する。これは樹脂のペレットに顔料を混ぜ合わせて色を付ける方法だ。ほかには、完成した色のマスターバッチを混ぜる方式、最初から着色されているペレットを用いる方式があるが、どちらも高価で管理する在庫も増えやすい。ドライカラー方式は技術力が必要ではあるが、コストが安くデザイナーからの色の要望に応えやすいなど、メリットが多いという。
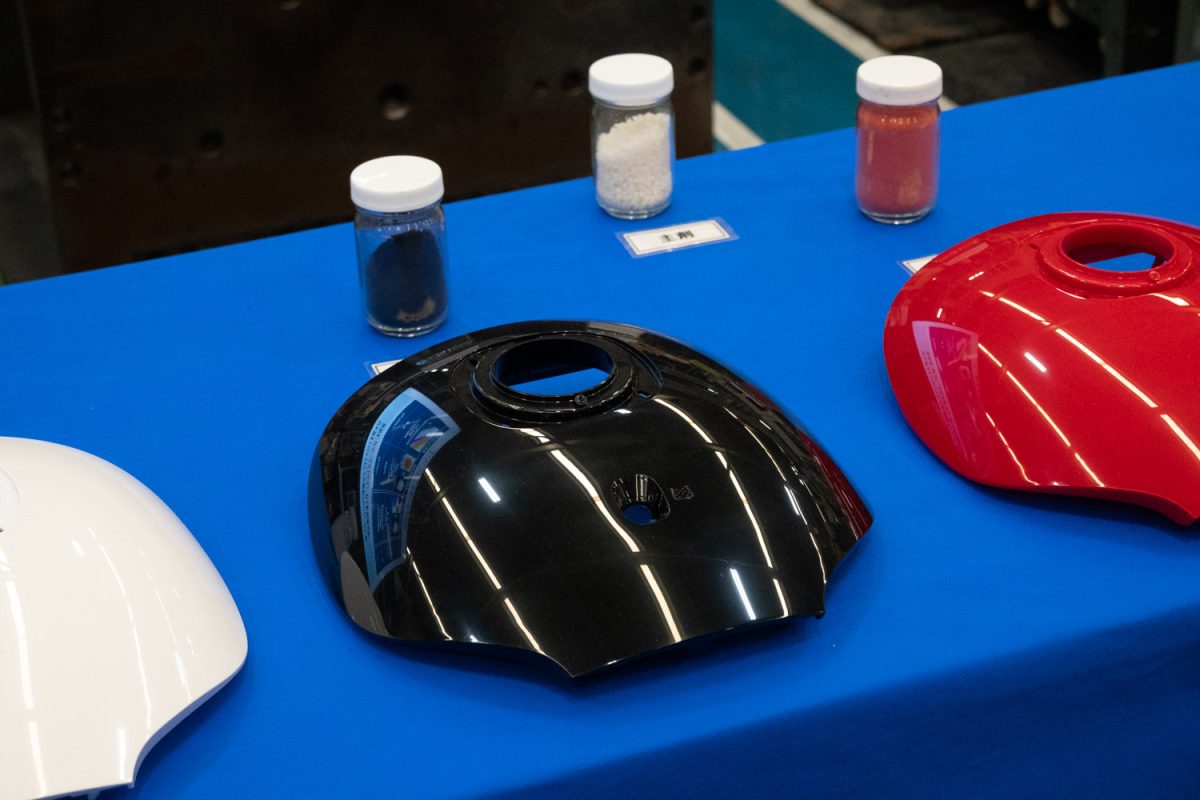
今回の取材では、床ノズルを成形する様子を見学。樹脂のペレットと顔料が配管を通って投入され、それをプレスして成形、冷却を行った後にベルトコンベアに流すまで自動で行う。クリーンドックの側面部分を作る様子も見ることができたが、こちらは整形した後にレーザー印刷をするところまでが自動化されていた。
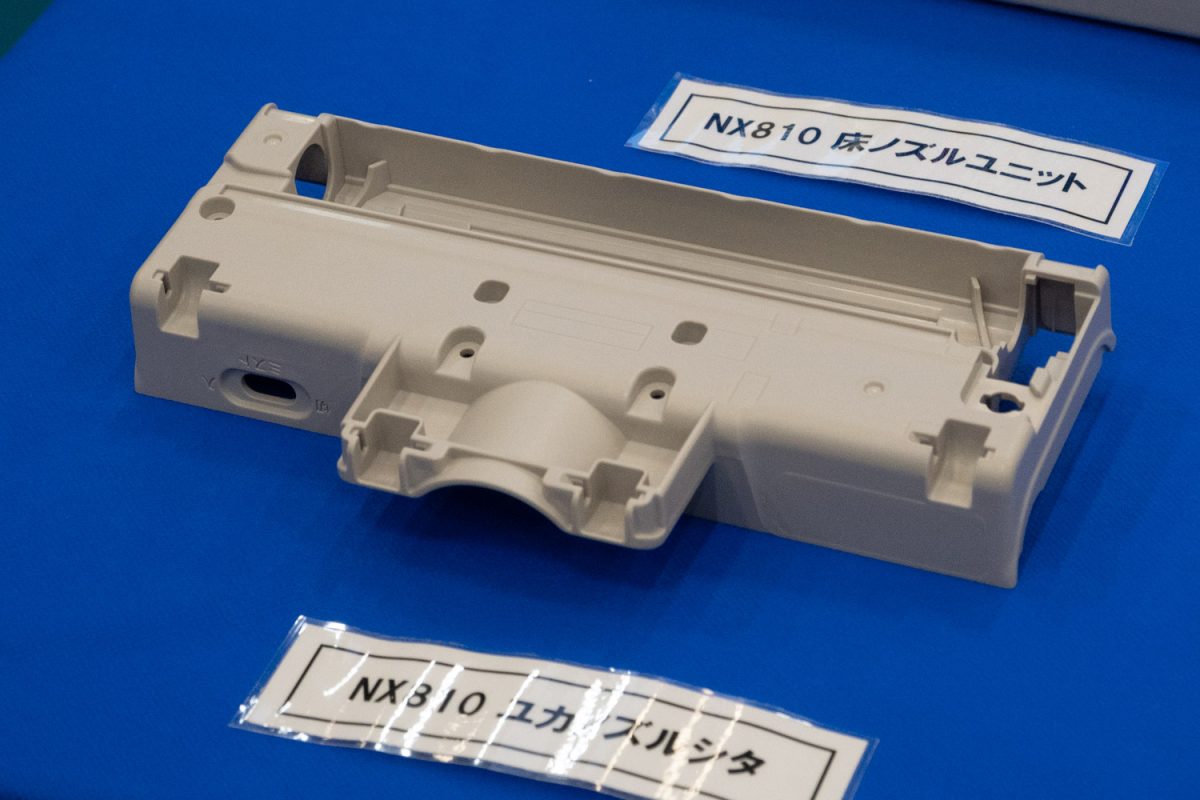
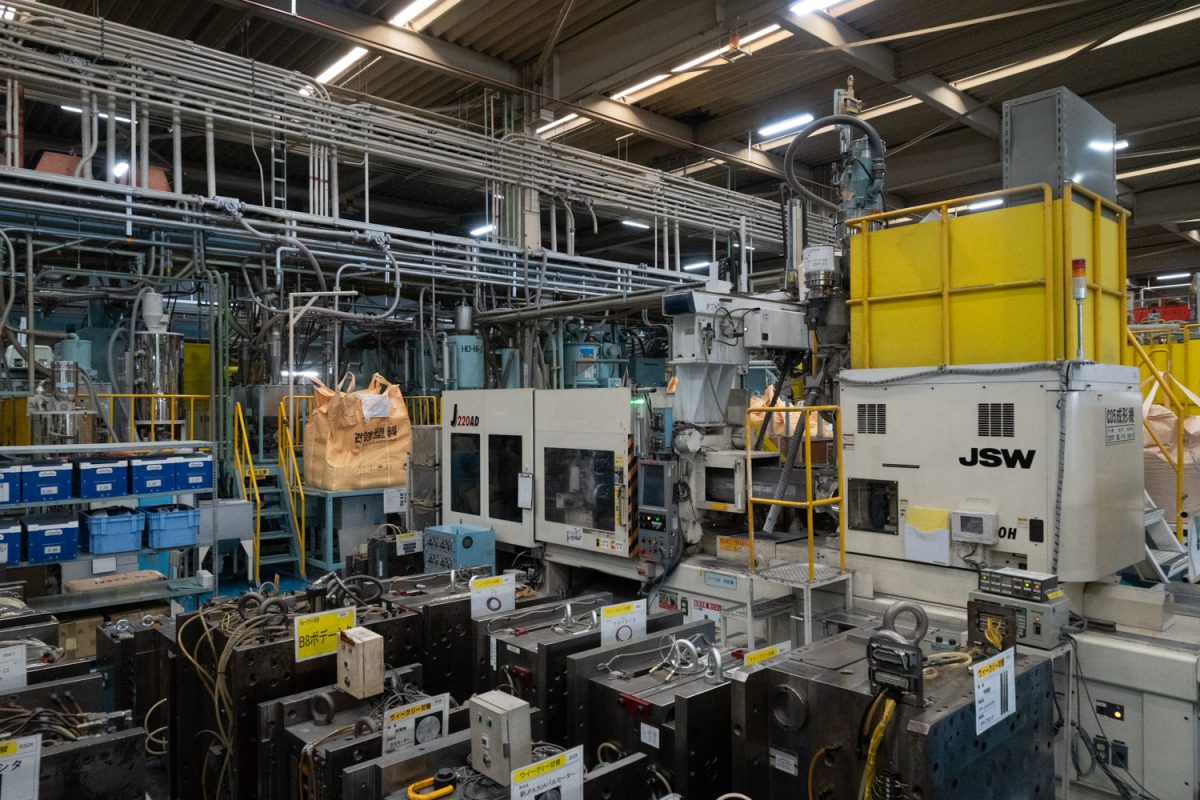
なお、本製品のクリーンドックの約60%は再生プラスチック材が使用されている。今回見学したクリーンドックの成形工程にも再生プラスチック材が使用されているが、成形中にガスが発生しやすく、通常の樹脂材料よりも技術やメンテナンスが必要とのこと。ガスが発生すると表面にガスヤケができたり、再生プラスチック材はそもそも金型にうまく流れにくいため、成形不良(ショートショット)が生じてしまう。だが、そういった問題も技術とノウハウで解決させている。
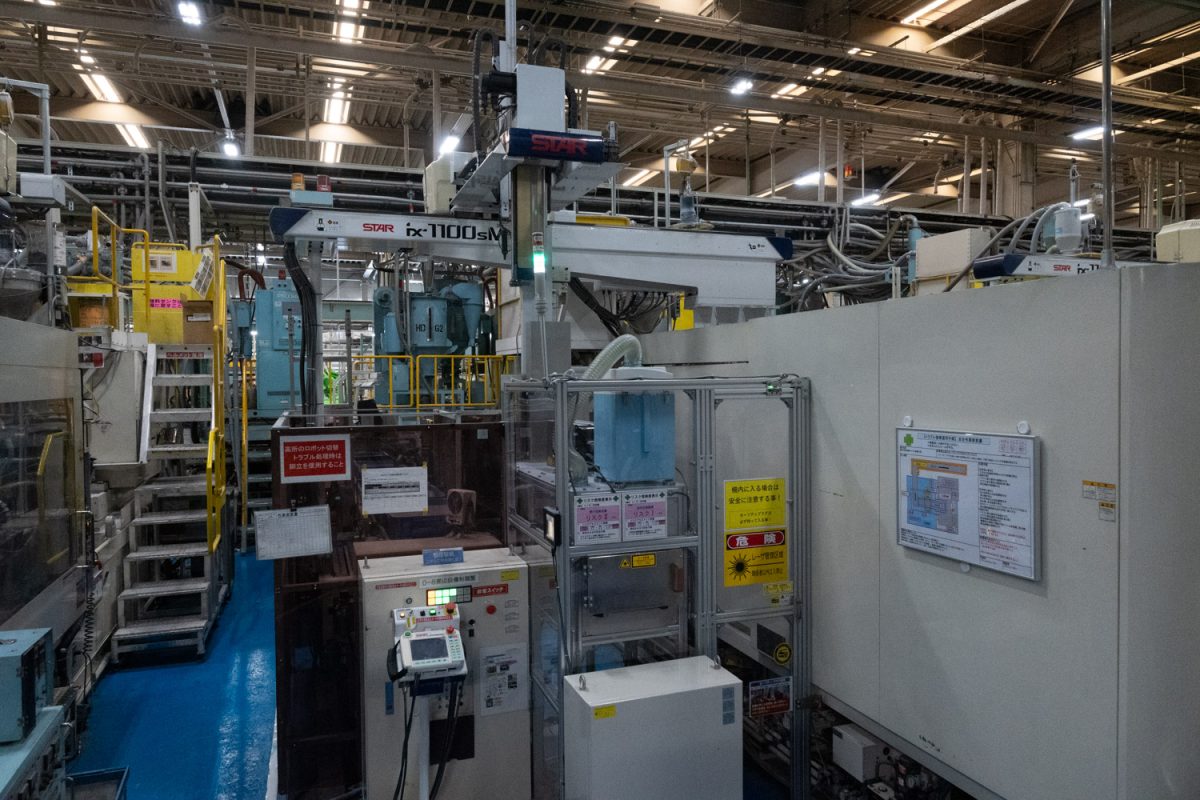
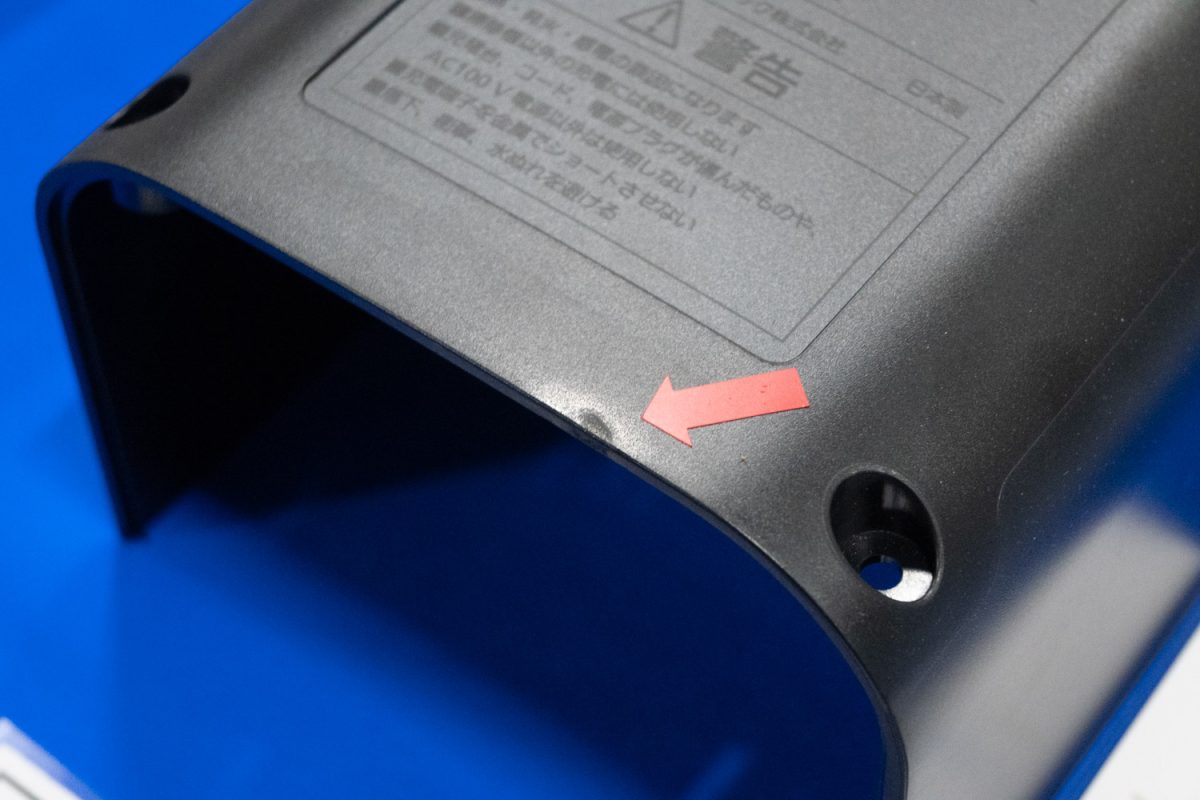
続いては、パーツを組み立てる工程。成形したパーツはベルトコンベアで自動的に運ばれてくるようになっている。成形しているエリアでは人の数も少なかったが、組み立てでは多くのスタッフが並んで作業しており、熟練の技術が品質を支えているとのこと。1つの工程が40秒という目安で区切られており、モーターの取り付けや配線なども人の手によって行われている。掃除機、クリーンドック、床ノズルは別のラインとなっており、特に床ノズルはパーツ点数が40点と多く、密度も高いので繊細な作業が要求されるとのこと。
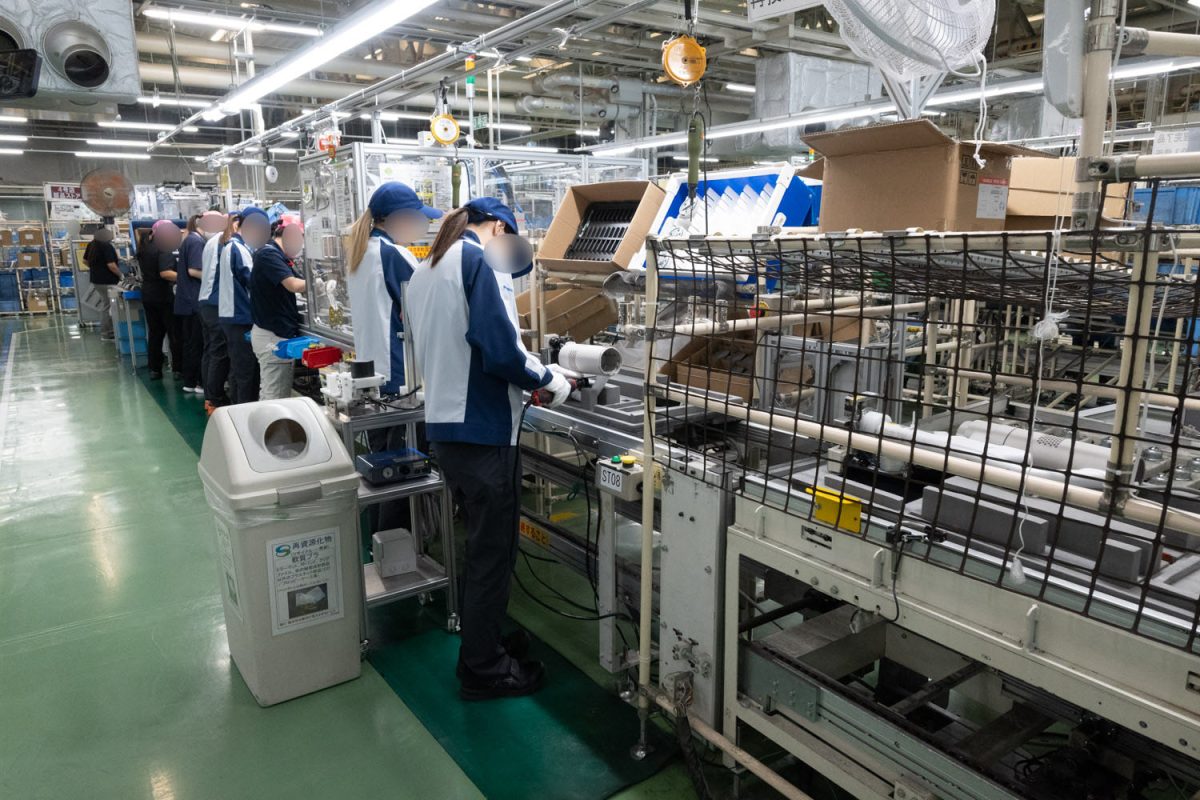
それぞれ組み立てが終わったあとは、電源を入れての検査が1品ずつ自動で行われる。詳しくは後述するが、別途製品をランダムに抜き取り、より詳しい検査も行っている。検査で規定の水準を満たしていれば梱包のラインに送られ、付属品とともに段ボール箱に詰められていく。ちなみに、梱包時にパーツの欠品を防ぐためのトリプルチェック体制が敷かれており、各パーツのピッキングをセンサー認識、梱包する様子を画像判定、そして梱包後には質量がチェックされる。
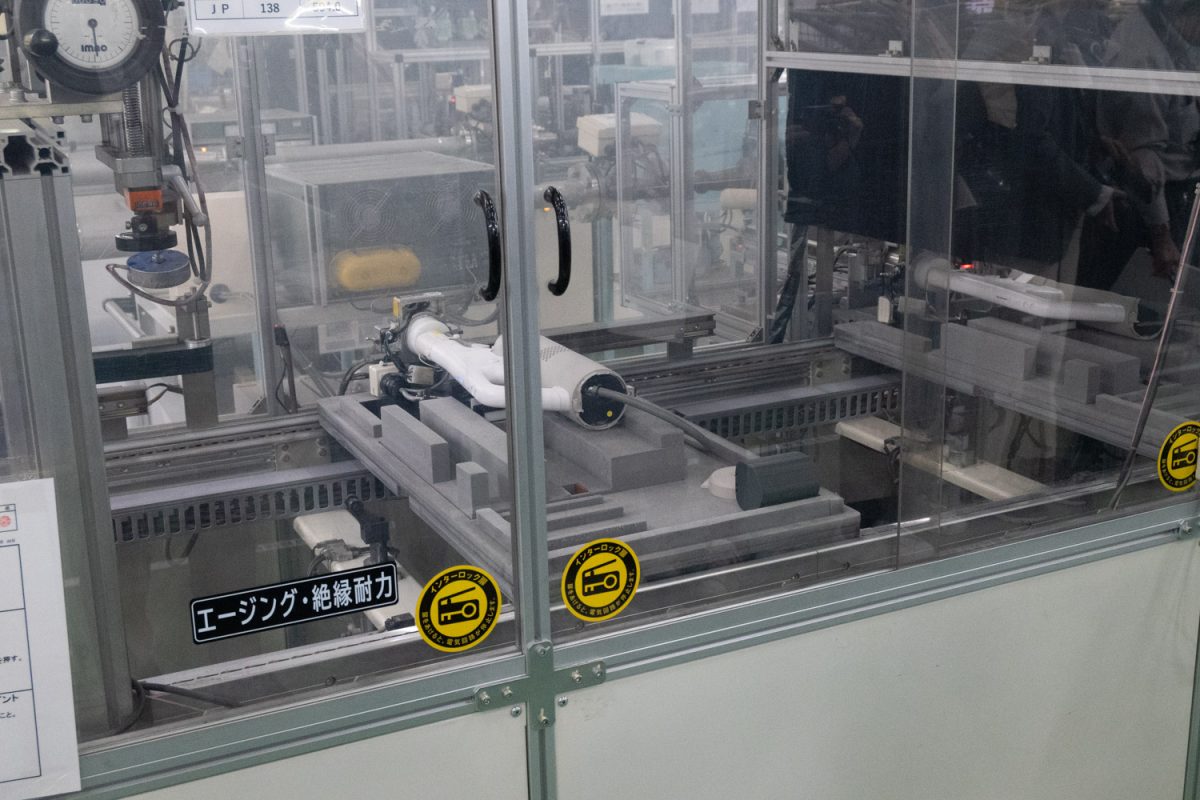
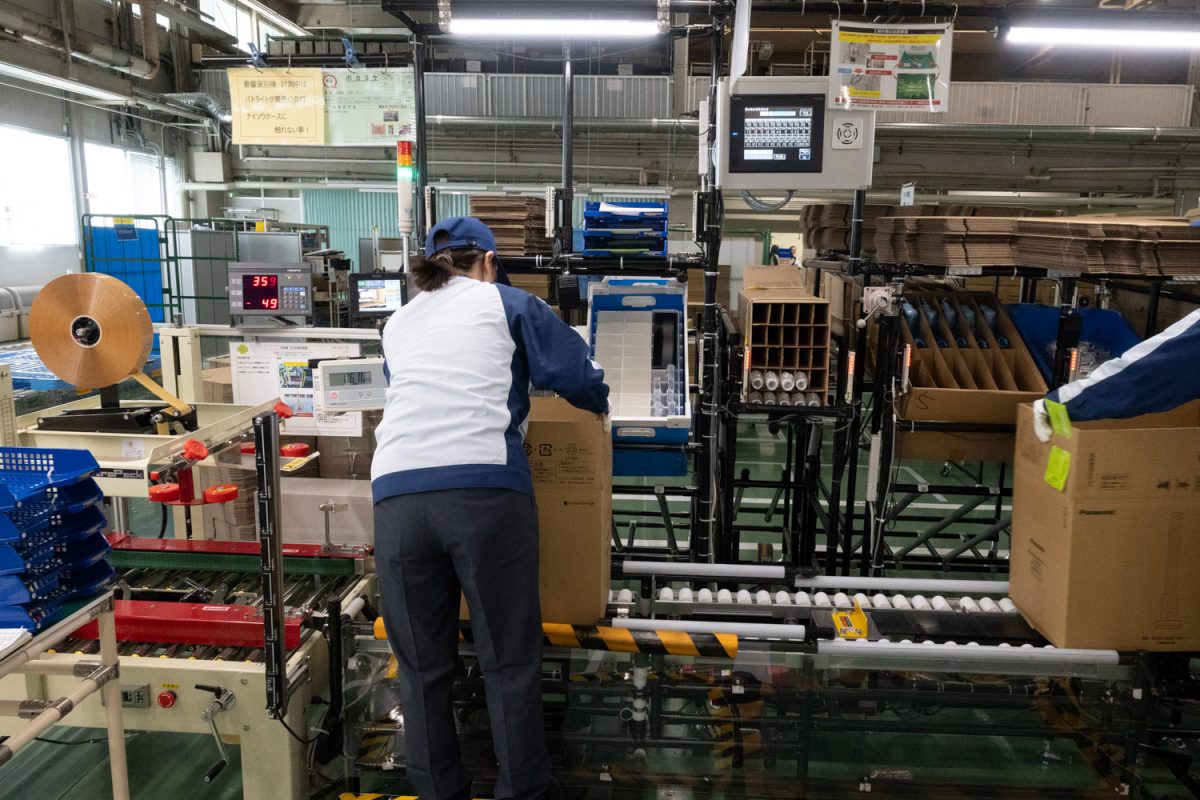
製品を抜き取って行う「完成品出荷検査」は、出荷検査室という専用の部屋で実施する。月あたり約250台をテストしているとのこと。絶縁耐力検査といった安全に影響するものから、吸込仕事率や騒音検査といった基本性能に関わるもの、さらにゴミすてボタンの操作性やアタッチメントの咬合といった使用性の部分まで、検査項目に入れられているという。
見学では、今回の製品の特徴である、マイクロミストの噴霧量を検査する様子が実演された。まずは水道水を20度に調整し、ヘッド部分にあるタンクに注水。そして1分間、動作する様子を目視でチェックし、出方にムラがないか等を確かめる。また、噴霧の前後で重さを計測することで、噴霧で減った水の量が規定以内かもチェックするそうだ。
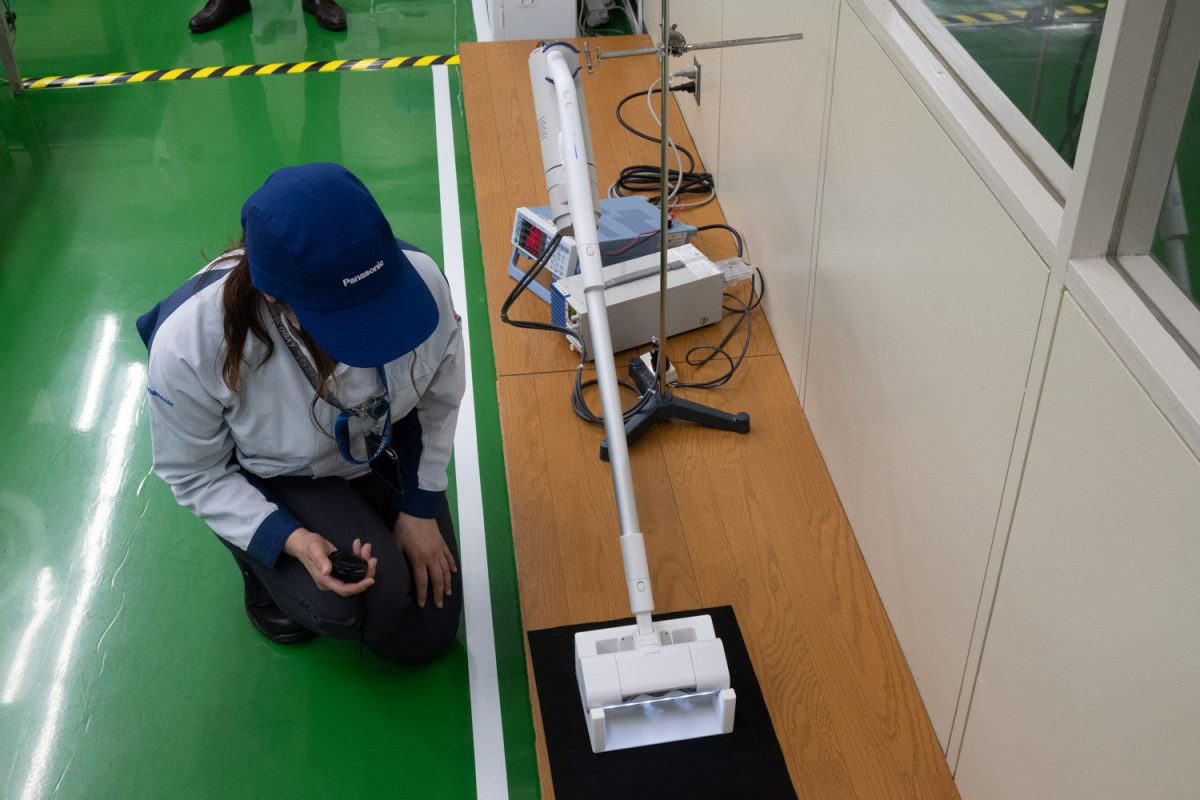
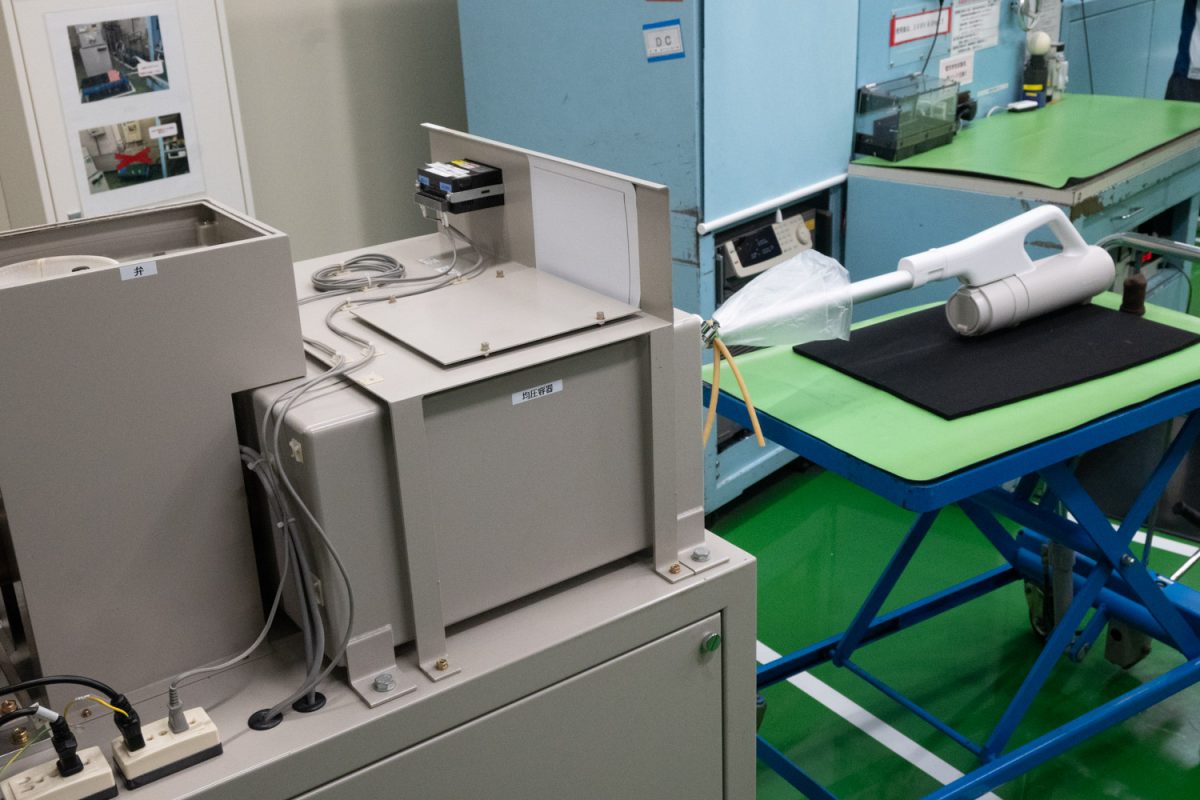
サステナビリティへの取り組みも推進
また、パナソニックでは2030年を目標に、CO2の排出量ゼロ化を目指している。八日市工場ではその目標を達成する取り組みとして、組立て棟の屋上に2,658枚、広さにしてテニスコート19面分の太陽光パネルを設置(2023年1月導入)。4人家族の場合で230軒分を発電し、組立て棟と製造棟の100%、工場全体で15%分の電力を太陽光から得ているという。第2弾のシステムも計画中であり、これからも目標に向けて推進中とのことだ。
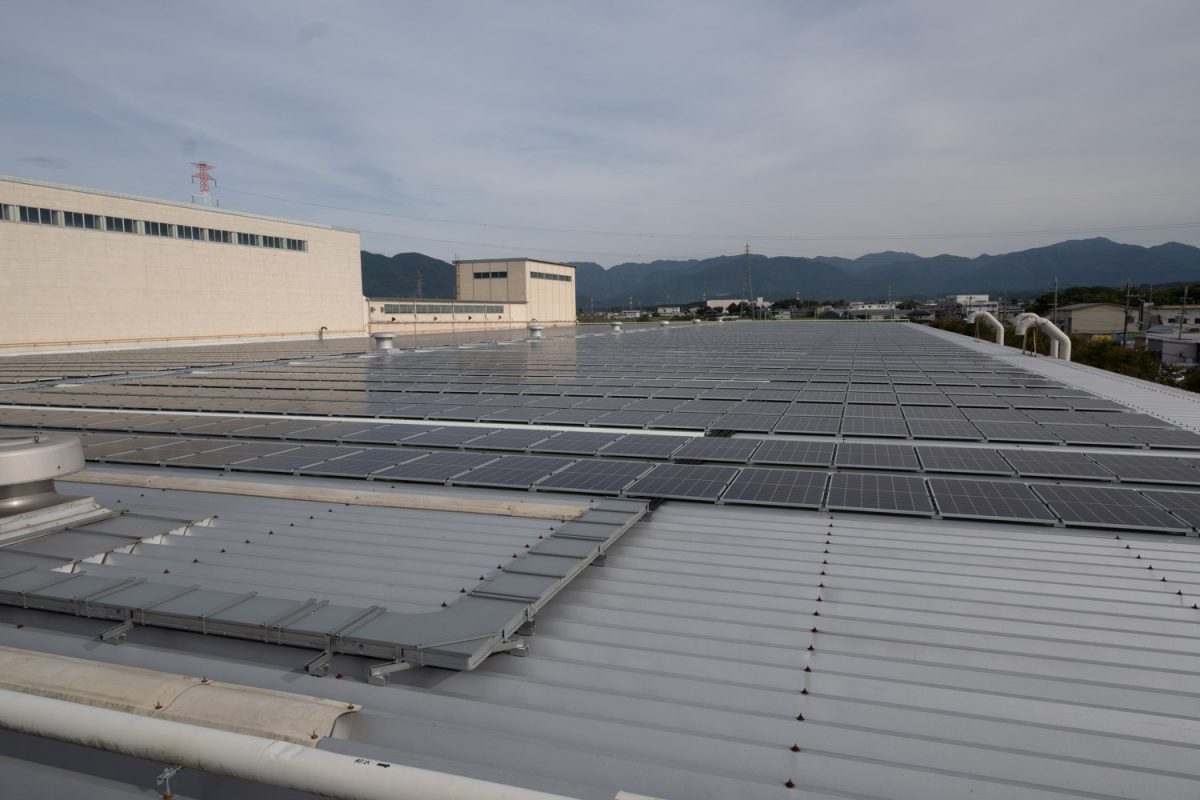
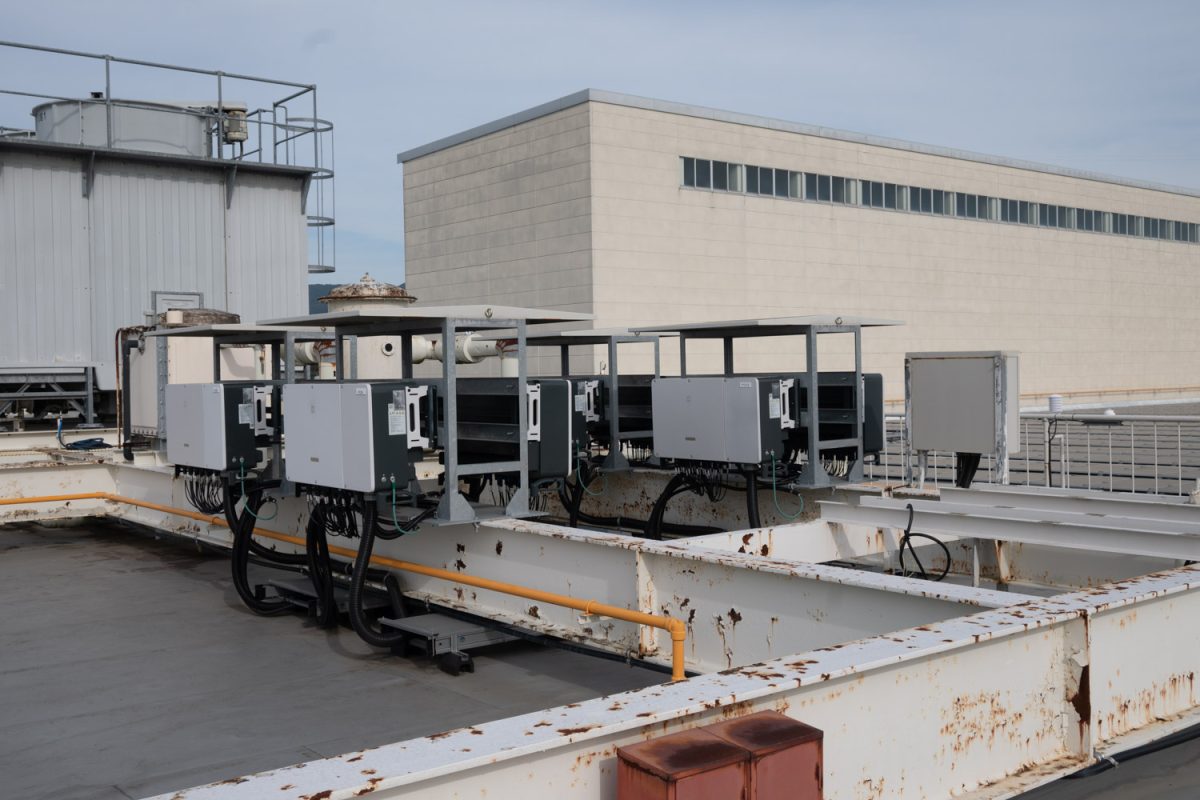
以上が、今回見学することができた、MC-NX810KMの製造現場だ。同社クリーナービジネスユニットの責任者である森下和久氏は、今回の製品は新しい清潔のスタンダードであり、同社が目指す「究極の提供価値の完成形」だという。そのうえで「これからも日本の住宅環境やあらゆる事態にしっかりと付き合い、掃除は嫌なものではなく、満足感・達成感を提供できる商品として開発していきたい」とも語っており、今後もどのようなアイデアが盛り込まれていくか楽しみだ。
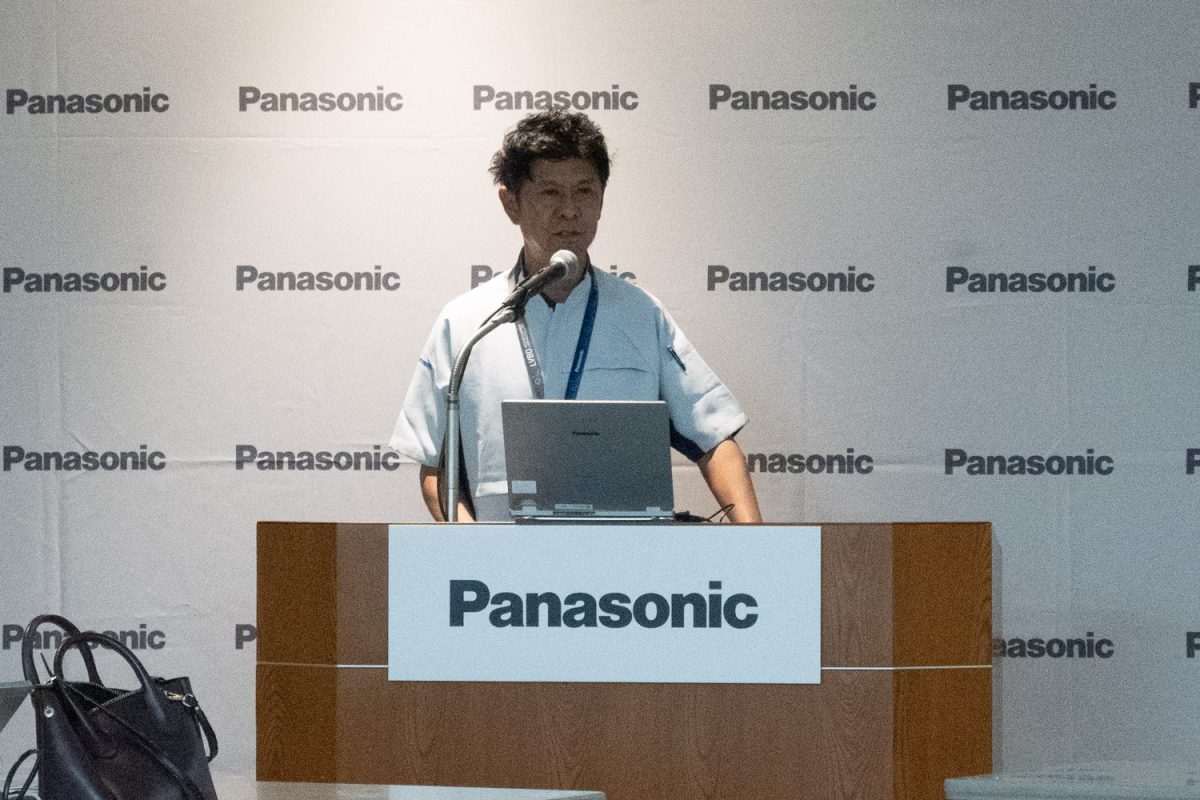